
Platform
for modern information systems and
industry 4.0
LOTYLDA is a platform developed by the Czech company OptiSolutions for the collection and analysis of data from production processes, maintenance management, logistics support and the creation of modern information systems with process automation based on BPM and RPM.
LOTYLDA is an ideal tool not only for technological and manufacturing companies that want to improve the quality of their processes and products, minimize risks and make operations more efficient. This platform provides accurate and reliable information about the status of entities and processes, which enables timely response to emerging problems and effective planning.
The use of deep learning brings an additional benefit in that algorithms learn from data and are able to identify patterns and trends that might otherwise remain hidden. This enables more efficient use of data and better decision making.
Overall, LOTYLDA is a powerful process improvement and risk management tool that can help businesses reduce costs and increase profitability.
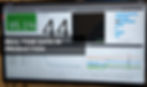



Data integration
Integration, analysis and visualization of TBs data
-
all data (machines, ERP, DB, EOLT, XLS) in one place
Data mining (LOTYLDA BI)
-
searching for nontrivial dependencies in data
Object recognition by Neural Networks (LOTYLDA DL)
-
product classification, quality control
Module for maintenance and terminal (LOTYLDA PMM)
-
reactive, planned and predictive maintenance
-
non-production states, material logistics
HTML5
-
available from PC, tablet, mobile
Paralell system
-
ability to run on multiple servers
-
uses the GPU
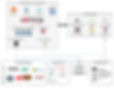
Quality Control


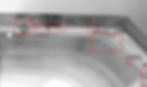

It is an Artificial Intelligence tool for advanced quality control or machine diagnostics. It uses machine vision and deep neural networks. Ideal for image, video, sound, or vibration recognition.
Neural networks are taught similarly to humans according to examples (patterns). Their advantage is the generalization capability, that they apply the learned knowledge to differing conditions from those under which they were taught
Business Intelligence / Information Systems
It is a technological online platform that enables the creation of information systems with an emphasis on the collection, storage and analysis of big data. The platform is accessible through a web browser (HTML5) and provides users with tools for creating ETL, data storage, reporting, analysis and prediction modules. One of the key features of this platform is the automation of defined processes at various levels.
This platform is suitable for organizations in various industries that need to manage their processes, analyze data and ensure easy connection to other systems such as ERP, accounting systems, production systems or registers. Thanks to its flexibility and customization options, the platform is an ideal solution for fintech systems, providers of financing, leasing, credit and loans as an effective tool for managing processes, requests, accesses, documents, entities, installment calculations, defining dependencies and comprehensive analysis and reporting.
The platform is also capable of creating a statistical application given thatall descriptive statistics are ready.Statistics use a parallel query.
Analysis
-
descriptive
-
predictive
-
time lines
Data mining with the implementation of the GUHA method.
Production and Maintenance
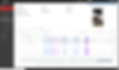
LOTYLDA PMM is an application manages and monitors human resources and machines and maintenance within the production area
PRODUCTION:
-
management and monitoring of operators, identification of operators, production lines and non-production processes
-
production plans and stoppage analysis
-
EOLT management, indicators measured by individual products
-
identification of possible defects for NOK analysis
MAINTENANCE:
-
maintenance monitoring and planning
-
machinery and its defects vs troubleshooting
-
defects analysis
-
predictive maintenance based on sensors data